
Aerodynamics Explained
Why having great aero is so important!

1. The Basics of Truck Aerodynamics
What are the basics of aerodynamics when it comes to trucks? Well, essentially it’s all about minimising the amount of exposed trailer / body bulkhead to the oncoming airflow as much as possible.
A truck and trailer travelling through the air creates drag. It is this drag which has an effect on the amount of fuel required to “push” the truck and trailer through the air. By minimising the drag as much as possible, can directly impact the amount of fuel consumed by the truck during its trip.
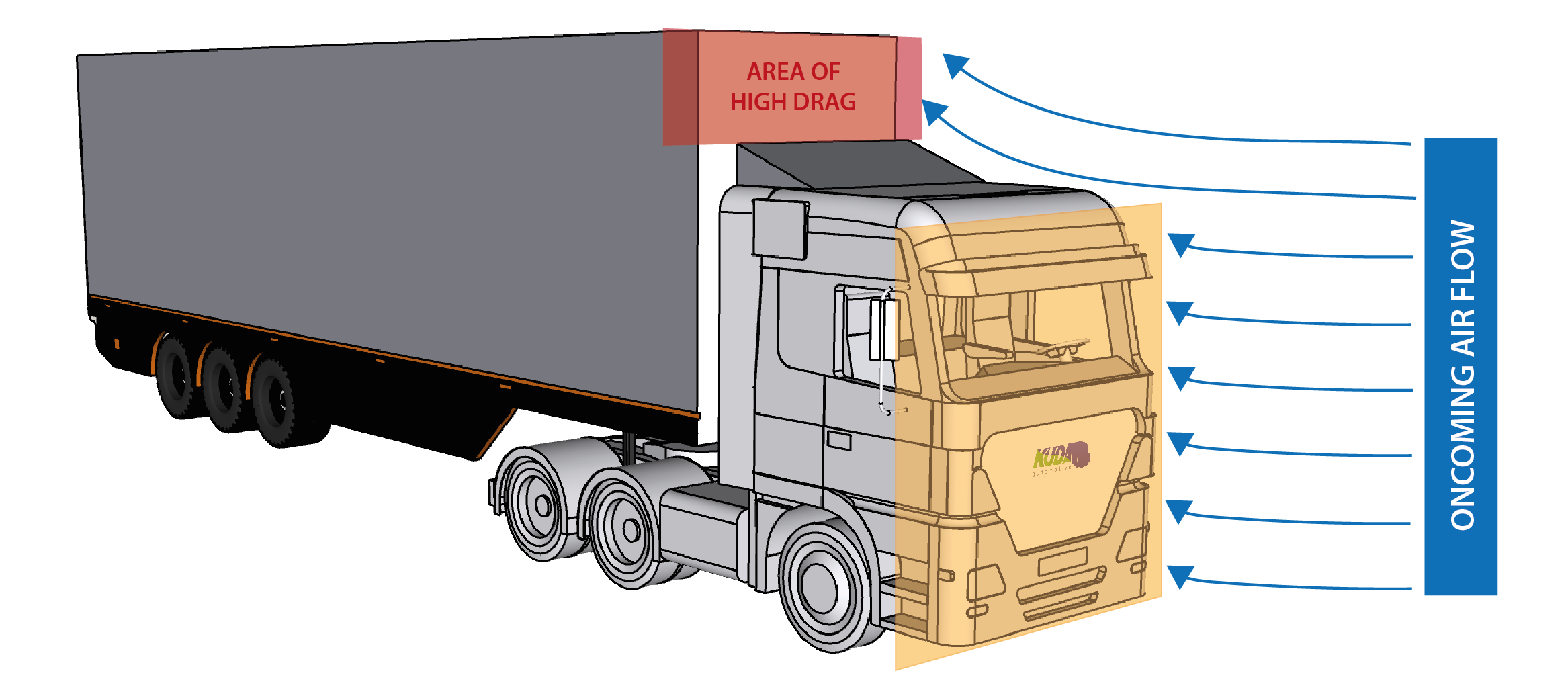
The uniqueness, and therefore greater importance of having great truck aerodynamics in the UK stems from the differing heights of trailers and bodies that are on UK roads.
In mainland Europe the maximum vehicle height does not exceed 4m, and therefore trucks and their air management packages from the factory are built to this height. In the UK however, operators frequently run trailers upwards of 4.2m to 4.6m and even 4.8m in height.


2. What does having "bad" aero cost?
Having the incorrect or a “bad” aerodynamic set up can, and is regularly costing fleet operators thousands of pounds, per truck, every single year. This cost can be easily quantified and calculated in relation to the amount of drag that could possibly be reduced from installing an air management kit to the vehicle.
The calculation is a relatively simple one, essentially for every 200mm of exposed bulkhead, drag on the vehicle increases by 3%. If you take a very standard set up of truck and trailer within the UK, running a 4m high tractor unit and a 4.6m high trailer, this equates to OVER £3,600 per truck, per year in excess fuel costs, which could be saved.

We have prepared some example figures of this calculation to demonstrate the cost per vehicle, based on the above mentioned set up and the current costs of Diesel fuel.


3. How to achieve "great" aero!
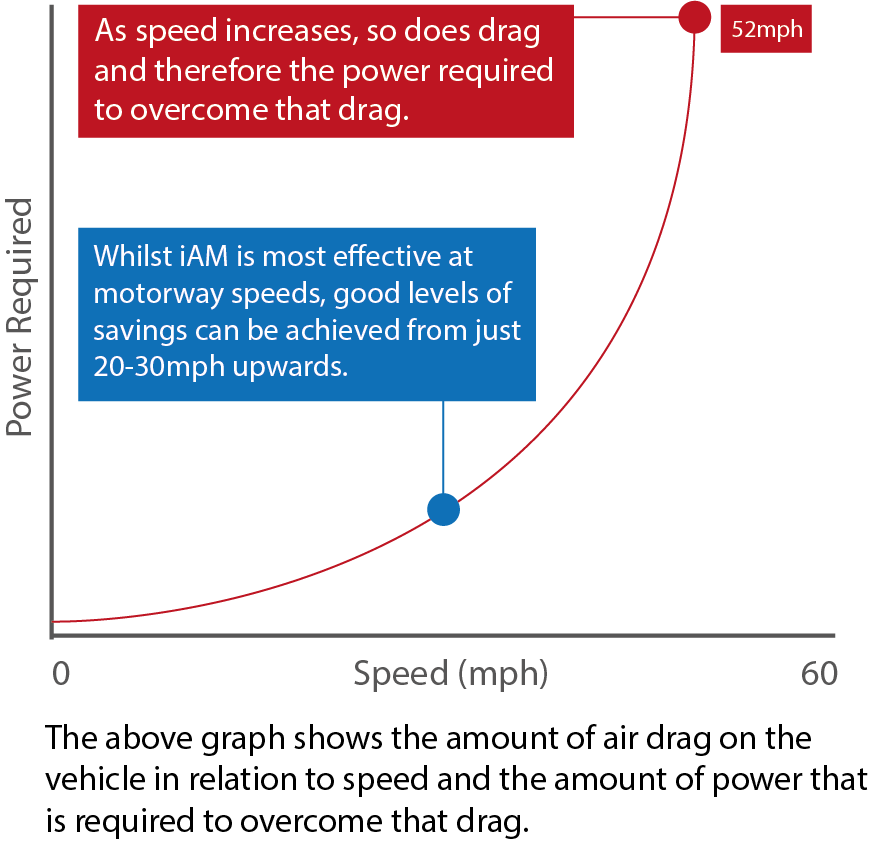
The answer to this, is very simple. Just reduce the area of exposed bulkhead as much as possible. The best way to do that is to install an air management system to “streamline” the gap between the top of the truck and trailer. Our iAM air management kit has a sleek, aerodynamic shape which allows for optimal airflow up and over the truck and trailer.
As the speed of the vehicle increases so does the drag. For example if you double your speed from 20mph to 40mph, you actually need up to 8 times the power to overcome the drag on the vehicle.
By reducing the area of exposed bulkhead with an air management kit, it is then possible to dramatically decrease the drag imposed on the vehicle and therefore the amount of power (fuel) required to drive through the oncoming air flow.


4. How Quick is the return on investment?
The cost of fitting an air management kit may seem daunting, however with the return on investment being achieved in as little as just 25 weeks in some cases, the cost can be offset relatively quickly in fuel savings.
Whilst the exact return on investment can vary, depending on a number of factors, such as the number of miles travelled annually, initial outlay and also fuel savings the below chart shows how a “typical” tractor unit running 100,000 miles a year, fitting an iAM air management system can see a return on investment in just 25 weeks.

